Software Modules that propel you forward
The Smart VibroAnalyzer 95 is the most powerful vibration analyzer currently on the market. - Whatever you want, the SVA 95 can do it!
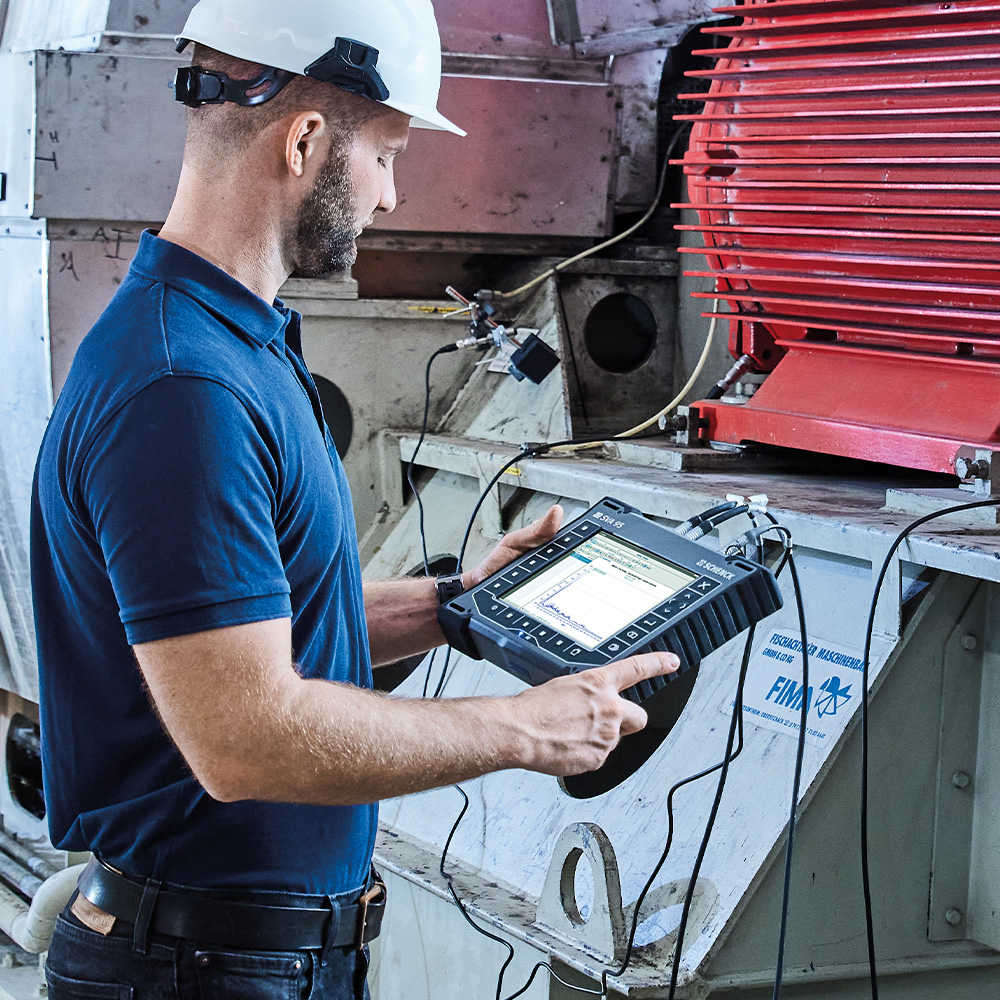
Vibration Analysis and Machine Diagnosis
Allow the Smart VibroAnalyzer 95 to be the expert for your balance of plant machines with the Diagnostic Module. The diagnostic module is standard in the SVA 95, enabling you to automatically detect machine faults such as unbalance, looseness, misalignment, and bearing faults.
If the ISO 10816 or user defined alarm limits are exceeded the Diagnostic Module will specify the faults and severity to detect the most common troublesome faults. If more detailed analysis is then needed to further diagnose the machine, additional measurements can then be taken from many available modules such as Analysis, Recorder, or Tracking, etc.
Extensive Analysis for all Operating Conditions
Early Detection and diagnosis of machine faults are key principles for planning and executing plant maintenance. With the Analysis Module, the user can select the type of measurement (from simple overall values to FFT’s and time signals, to more advanced measurements such as orbits using displacement/proximity probes) and set up multiple, synchronized, simultaneous measurements from all channels with settings such as frequency range, sampling rates and units.
The Smart VibroAnalyzer 95 feature frequency ranges of: 0.35 Hz to 90 Khz (194 kHz sampling), respectfully, to identify most faults.
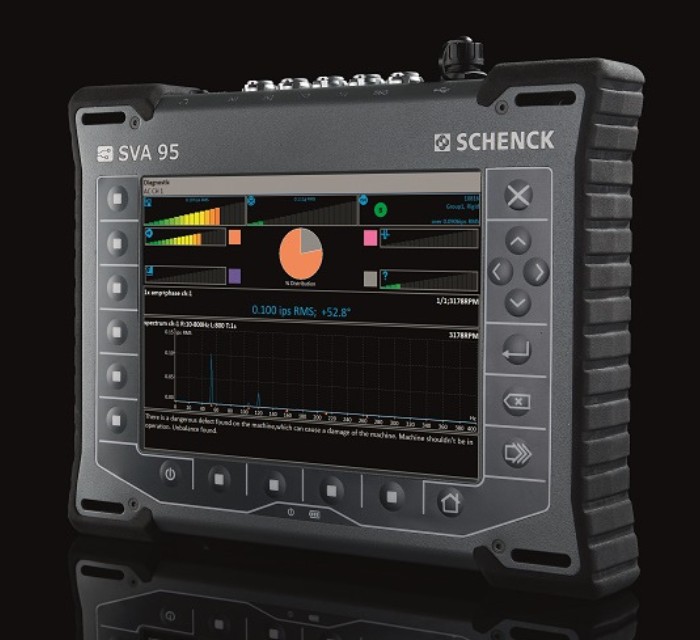
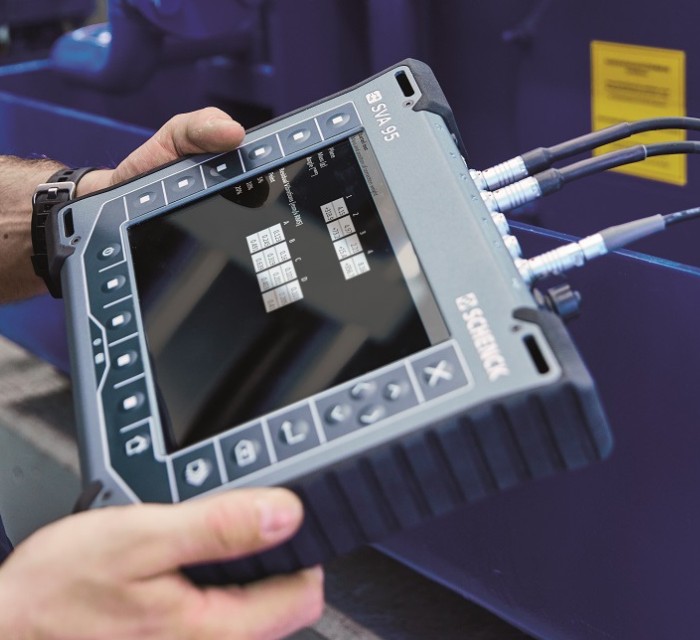
Assessment of roller bearings
Using the Analysis or Recorder Modules, envelope spectrum analysis can be performed, which detects periodic impacts resulting from roller bearing and gearing damage. The analysis is based on demodulating amplitude-modulated vibration signals such as EDS (Envelope Detection Signal) and BDS (Bearing Detection Signal). By utilizing this feature, you can plan ahead and take necessary measures at an affordable cost.
In addition, the Lubrication Greasing Control module can be used to monitor and control the lubrication process of the bearings. Both a lack or excess of lubricant is harmful to a rolling element bearing. This module measures the actual bearing lubrication status and informs the operator when the lubrication state is optimal, relative to programmed lubrication guidelines.
In-depth vibration analysis
IIf more detailed vibration analysis is needed, the Recorder Module allows the user to record live data from a machine and perform post-processing of the data on the unit itself. The user can perform post-processing of the same raw timewave form multiple times allowing for a more precise analysis of a detected fault to determine the location and severity.
In addition, the data can be transferred to a host computer with the Schenck Diagnostic Center Software for reporting.
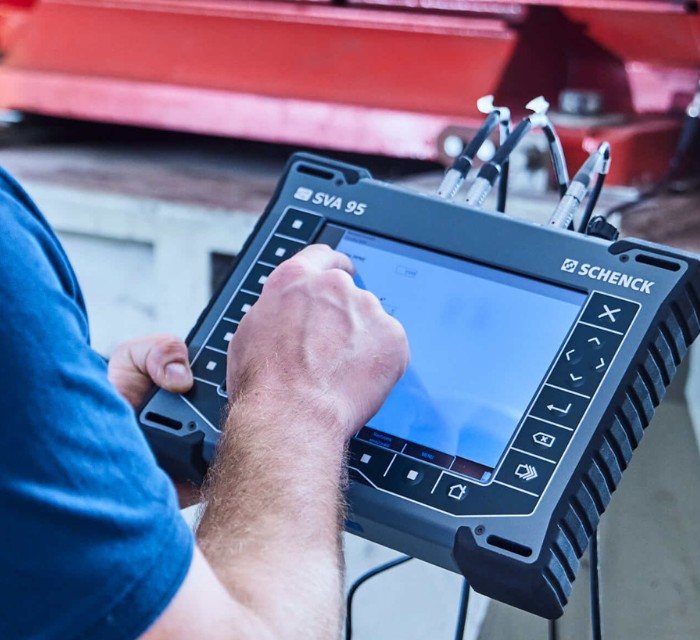
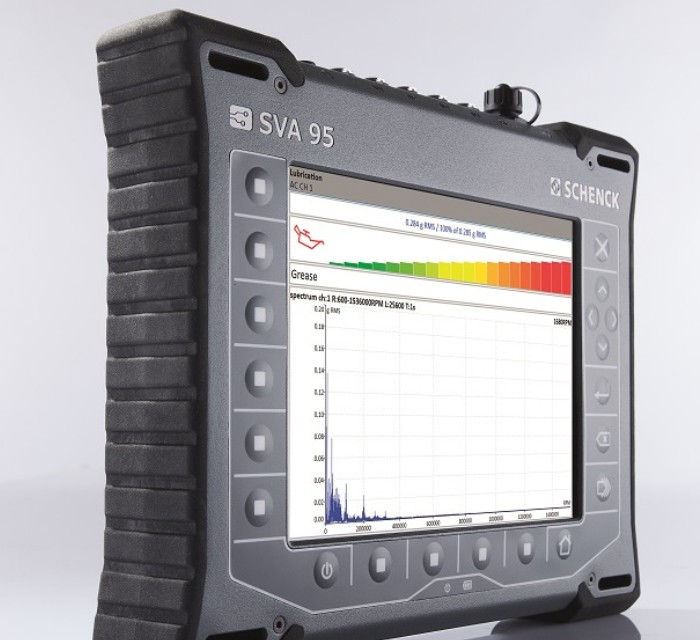
Sound Vibration at its finest
With the Octave Analysis Module, you can measure audible sounds by connecting a microphone to the Smart VibroAnalyzer 95. Measure sound levels and octave spectrums with selectable resolutions of 1/1, 1/3, 1/12, or 1/24.
Need to measure sounds inaudible to the human ear such as air leaks, electrical arcing, or early bearing fault detection? The Ultrasound module in combination with a microphone allows the Smart VibroAnalyzer 95 to do just that. In addition, the Smart VibroAnalyzer 95 can also be connected to a standard set of headphones using the stethoscope module to listen to vibrations, which can be recorded and replayed.
Early elimination of potential hazards
The bump test determines the natural frequencies of a machine system. In the context of a rotating machine, this pertains to those ranges of rotational speeds within which vibrations are disproportionately amplified due to resonances, posing the potential to damage the machine.
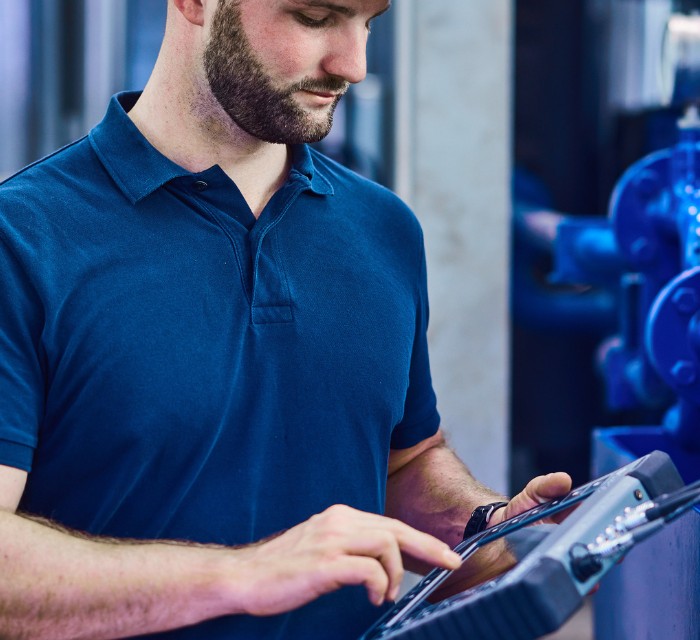
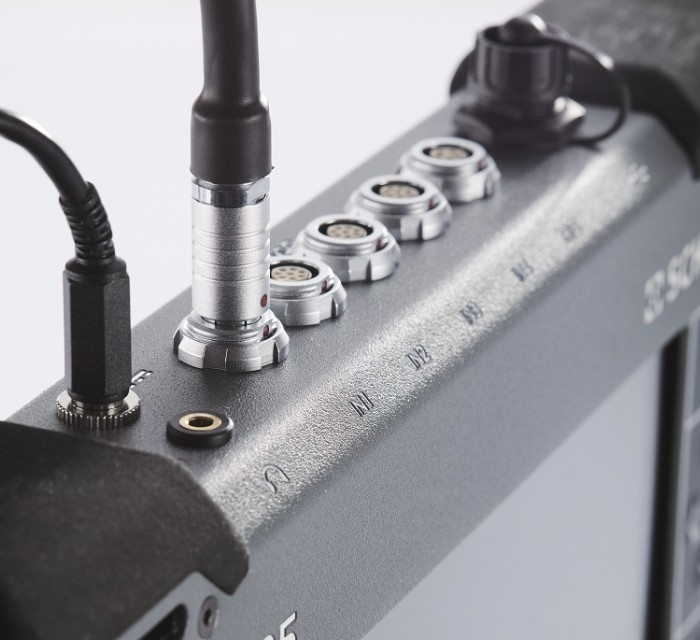
Avoid Unbalances in your Operations
The Smart VibroAnalyzer 95 also includes an Advanced Balancer Module that supports muti-plane balancing of up to eight (8) planes balancing on flexible or rigid rotors. Multi-plane is used for rotors with complex geometries that exhibit significant unbalance in multiple planes. In addition, the Advanced Balancer Module can assist with complicated jobs where the number of measurement points is larger than the number of correction planes available.
Clearly discerning machine resonances (optional)
With the Tracking Module, resonances in the system can be determined by the measurement and graphical display of the amplitude and phase angle of the rotational vibrations as a function of the speed. The Tracking Module uses the raw vibration signal and visualizes the amplitude and phase angle in a bode, Nyquist, FFT waterfall diagram, and numerical reading. This ensures dedicated balancing outside the range of machine resonances. (This module is not part of the basic equipment).
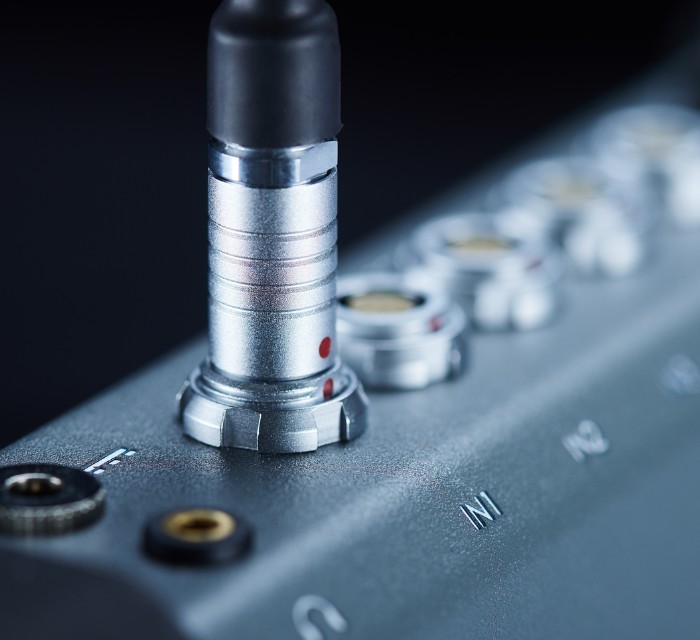
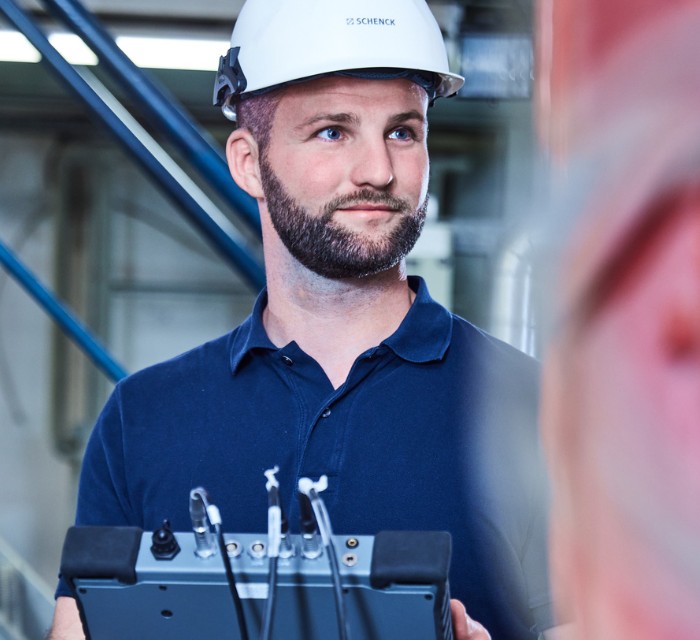
Route-based machine management (optional)
One of the fundamental principles of condition monitoring is data collection based on predefined alarm limits. The Data Collection module is used for the periodic collection of vibration data of the balance of plant machinery. Simply create a route tree with measurement points and locations in the Schenck Diagnostic Center Software and upload the route in the Smart VibroAnalyzer 95. With the uploaded route you are prompted by the unit to move from machine to machine with specific measurement points to efficiently collect data.
The Smart VibroAnalyzer 95 will notify you of an alarm situation that can easily be reviewed on the unit to provide onsite feedback. After the route is completed, the collected data can be transferred back to the Schenck Diagnostic Center Software via USB-C cable to store readings, review trends, analyze data, and provide reports.
Avoid Unbalances in your Operations
New rotors may initially be balanced, before their first use, but their balance can be disrupted or affected due to various factors such as installation, wear, and operational influences. These unbalances can result in mechanical vibrations during use, which can cause premature wear of bearings, fatigue, force fractures, or shaft deformations. Fortunately, our Smart VibroAnalyzer 95 allow for highly accurate balancing of rotors in their installed condition without requiring machine dismantling. And this can be accomplished in 1 or 2 plane corrections operating at rotational speeds ranging from 30 to 250,000 RPM.